Automatic Warning System
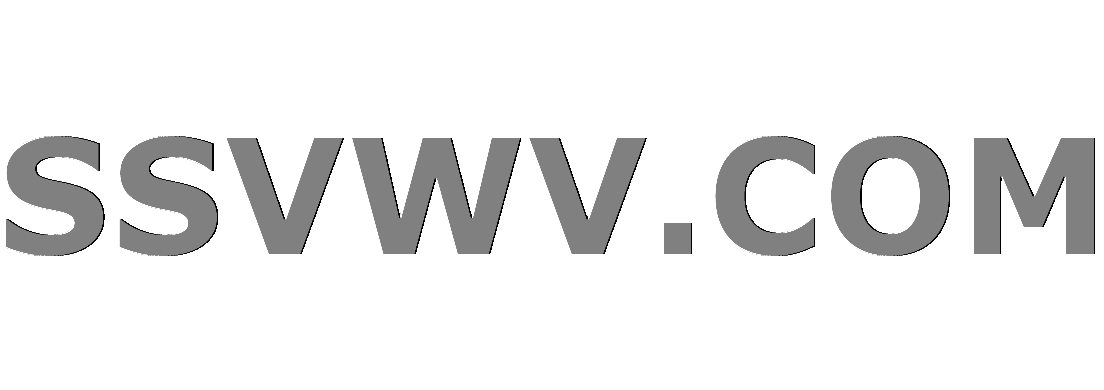
Multi tool use

The AWS indicator inside Class 27 showing caution.
The Automatic Warning System (AWS) was introduced in 1956 in the United Kingdom to provide a train driver with an audible warning and visual reminder that they were approaching a distant signal at caution.[1]
Its operation was later extended to give warnings for;[2]
- A colour light signal displaying a double yellow (steady or flashing), single yellow or red aspect
- A reduction in permissible speed
- A temporary or emergency speed restriction
- An automatic barrier crossing locally monitored (ABCL), an automatic open crossing locally monitored (AOCL), or an open crossing (OC).
AWS was based on a 1930 system developed by Alfred Ernest Hudd (ca. 1883-1958)[3] and marketed as the "Strowger-Hudd" system. An earlier contact system, installed on the Great Western Railway since 1906 and known as automatic train control (ATC), was gradually supplanted by AWS within the Western Region of British Railways.
Contents
1 Principles of operation
1.1 AWS at signals
1.2 AWS for speed warnings
2 History
2.1 Early devices
2.2 GWR automatic train control
2.3 Strowger–Hudd system
3 Network Rail
3.1 Expansion of AWS application
3.2 Limitations
4 Bi-directional operation
5 Liberia
6 Other countries
7 See also
8 References
8.1 Literature
9 Further reading
Principles of operation

Driver's AWS equipment in a Class 43 driving cab
Information is conveyed by electromagnetic induction to the moving train through equipment fixed in the middle of the track, known as an AWS magnet.[1] The system works by the train detecting sequences and polarities of magnetic fields passing between the track equipment and the train equipment via a receiver under the train.[1] Multiple unit trains have a receiver at each end. Vehicles that can operate singly (single car DMUs and locomotives) only have one. This could be either at the front or rear depending on the direction the vehicle is travelling in.
The equipment on a train consists of;
- A magnetically operated 'receiver' underneath the front of the train
- A relay control box
- A visual indicator (known colloquially as a 'sunflower')
- An audible sounder which produces either a 'horn' or 'bell' sound
- An AWS/TPWS acknowledgement button[1]
- An AWS/TPWS Driver Machine Interface (indicator panel)[4]
- An interface with the train's emergency braking system
- A static voltage-converter providing operating voltages of 12 V and 40 V from the unit supply
- An isolating switch to disconnect the AWS for maintenance or if the AWS develops a fault in service
AWS at signals

An AWS/TPWS Driver machine interface
As the train passes over an AWS magnet, the 'sunflower' indicator in the driver's cab will change to all black. If the signal being approached is displaying a 'clear' for a semaphore or green for a multiple aspect colour light signal, the AWS will sound a bell (modern locomotives/multiple units use an electronic sounder that gives a distinctive 'ping') and leave the visual indicator black. This lets the driver know that the next signal is showing 'clear' and that the AWS system is working.
If the signal being approached is displaying a restrictive aspect (red, yellow or double yellow in colour-light installations or a distant semaphore at caution (horizontal)), the AWS will sound a horn. The driver then has approximately 2 seconds to cancel the warning by pressing and releasing the AWS/TPWS acknowledgement button (if a driver should collapse onto the button or keep it held down, the AWS will not be cancelled).[1] On cancelling the warning, the horn then stops and the visual indicator changes to a pattern of black and yellow spokes, which persists until the next AWS magnet and reminds the driver that they have cancelled the AWS.
As a fail-safe mechanism, if the driver fails to cancel the warning in time, the emergency brake will apply and bring the train to a stand. When this occurs the red Brake demand light will flash[4] on the AWS/TPWS Driver machine interface. The driver must now push the AWS/TPWS acknowledgement button, and the brakes will release after a safety time out period has elapsed.
AWS is provided at most main aspect signals on running lines, though there are some exceptions:[1]
- At through stations where the permitted speed is 30 mph or less and the layout is complex. Where this occurs, these are called AWS gap areas.
- AWS magnets are not provided at semaphore stop signals.
- Where a line is not fitted with AWS magnets, it is shown in the Sectional Appendix.

Temporary speed restriction warning board
AWS for speed warnings
The system works in the same way as for signals, except that a fixed magnet positioned between the running rails is located at the service braking distance before the speed reduction. The single magnet will always cause a horn (caution) to sound in the cab, which the driver must cancel to prevent the emergency brake applying. Beyond the magnet, a lineside warning board will advise the driver of the speed requirement ahead.
History
Early devices

Berlin S-Bahn train stop in its engaged (left) and disengaged (right) position
Early devices used a mechanical connection between the signal and the locomotive. In 1840, the locomotive engineer Edward Bury experimented with a system whereby a lever at track level, connected to the signal, sounded the locomotive's whistle and turned a cab-mounted red lamp. Ten years later, the redoubtable Colonel William Yolland of the Railway Inspectorate was calling for a system that not only alerted the driver but also automatically applied the brakes when signals were passed at danger but no satisfactory method of bringing this about was found.
In 1873, United Kingdom Patent No. 3286 was granted to C. Davidson and C.D. Williams for a system in which, if a signal was passed at danger, a trackside lever operated the locomotive's whistle, applied the brake, shut off steam and alerted the guard. Numerous similar patents followed but they all bore the same disadvantage – that they could not be used at higher speeds for risk of damage to the mechanism – and they came to nothing. In Germany, the Kofler system used arms projecting from signal posts to connect with a pair of levers, one representing caution and the other stop, mounted on the locomotive cab roof. To address the problem of operation at speed, the sprung mounting for the levers was connected directly to the locomotive's axle box to ensure correct alignment. When Berlin's S-Bahn was electrified in 1929, a development of this system, with the contact levers moved from the roofs to the sides of the trains, was installed at the same time.
The first useful device was invented by Vincent Raven of the North Eastern Railway in 1895, patent number 23384. Although this provided audible warning only, it did indicate to the driver when points ahead were set for a diverging route. By 1909, the company had installed it on about 100 miles of track. In 1907 Frank Wyatt Prentice patented a radio signalling system, using a continuous cable laid between the rails to relay "Hertzian Waves" to the locomotive.[5] The signal was turned off if the block were not "clear", a white or green light in the cab then turned to red and the brakes were applied. The LSWR installed the system on its Hampton Court Branch in 1911, but shortly after removed it when the line was electrified.[6]
GWR automatic train control
The first system to be put into wide use was developed in 1905 by the Great Western Railway and protected by UK patents 12661 and 25955. Its benefits over previous systems were that it could be used at high speed and that it sounded a confirmation in the cab when a signal was passed at clear.
In the final version of the GWR system, the locomotives were fitted with a solenoid-operated valve into the vacuum train pipe, maintained in the closed position by a battery. At each distant signal, a long ramp was placed between the rails. This ramp consisted of a straight metal blade set edge-on, almost parallel to the direction of travel (the blade was slightly offset from parallel so in its fixed position it would not wear a groove into the locomotives' contact shoes), mounted on a wooden support. As the locomotive passed over the ramp, a sprung contact shoe beneath the locomotive was lifted and the battery current holding closed the brake valve was broken. In the case of a clear signal, current from a battery energising the ramp (but at opposite polarity) passed to the locomotive through the contact and maintained the brake valve in the closed position, with the reversed-polarity current ringing a bell in the cab. When the signal was at 'danger', the ramp battery was disconnected and so could not replace the locomotive's battery current: the brake valve solenoid would then be released and a horn sounded in the cab. The driver was then expected to cancel the warning and apply the brakes under his own control.
Notwithstanding the heavy commitment of maintaining the batteries in the locomotives and signal boxes, the GWR installed the equipment on all its main lines. For many years, Western Region (successors to the GWR) locomotives were dual fitted with both GWR ATC and BR AWS system.
Strowger–Hudd system
By the 1930s, other railway companies, under pressure from the Ministry of Transport, were considering systems of their own. A non-contact method based on magnetic induction was preferred, to eliminate the problems caused by snowfall and day-to-day wear of the contacts which had been discovered in existing systems. The Strowger-Hudd system of Alfred Hudd, which used a pair of magnets, one a permanent and one an electro-magnet, was tested by the Southern Railway, London and North Eastern Railway and the London, Midland and Scottish Railway but these trials came to nothing.
In 1948 Hudd, now working for the LMS, equipped the London, Tilbury and Southend line, a division of the LMS, with his system. It was successful and British Railways developed the mechanism further by providing a visual indication in the cab of the aspect of the last signal passed. In 1956, the Ministry of Transport evaluated the GWR, LTS and BR systems and selected the one developed by BR as standard for Britain's railways. This was in response to the Harrow and Wealdstone accident in 1952.[7]
Network Rail
Network Rail (NR) AWS consists of:
- A permanent magnet set centrally between the rails and usually positioned such that it is encountered before the signal to which it relates. The top of the magnet casing is nominally level with the running surface of the rails.
- An electromagnet between the rails (with opposite polarity to the permanent magnet) positioned after the permanent magnet. Again the top of the casing is nominally level with the running surface of the rails.
- A cab indicator that can show a black disk or a yellow and black "exploding" disk, known as the "AWS sunflower"
- A control unit that connects the system to the brakes on the train
- A driver's AWS acknowledgement button
- An AWS control panel
The system works on a set/reset principle.
When the signal is at 'clear' or green ("off"), the electro-magnet is energised. As the train passes, the permanent magnet sets the system. A short time later, as the train moves forward, the electromagnet resets the system. Once so reset, a bell is sounded (a chime on newer stock) and the indicator is set to all black if it is not already so. No acknowledgement is required from the driver. The system must be reset within one second of being set, otherwise it behaves as for a caution indication.
An additional safeguard is included in the distant-signal control wiring to ensure the AWS "clear" indication is only given when the distant is proved "off" – mechanical semaphore distants have a contact in the electromagnet coil circuit closed only when the arm is raised or lowered by at least 27.5 degrees. Colour-light signals have a current sensing relay in the lamp lighting circuit to prove the signal alight, this is used in combination with the relay controlling the green aspect to energise the AWS electro-magnet. In a Solid State Interlocking the signal module has a "Green-Proved" output from its driver electronics that is used to energise the electromagnet.
BR Standard Strength AWS track equipment
When the distant signal is at 'caution' or yellow (on), the electro-magnet is de-energised. As the train passes, the permanent magnet sets the system. However, since the electro-magnet is de-energised, the system is not reset. After the one-second delay within which the system can be reset, a horn warning is given until the driver acknowledges by pressing a plunger. If the driver fails to acknowledge the warning within 2.75 seconds, the brakes are automatically applied. If the driver does acknowledge the warning, the indicator disk changes to yellow and black, to remind the driver that he has acknowledged a warning. The yellow and black indication persists until the next signal and serves as a reminder between signals that the driver is proceeding under caution. The one-second delay before the horn sounds allows the system to operate correctly down to speeds as low as 1.75 miles per hour. Below this speed, the caution horn warning will always be given, but it will be automatically cancelled when the electromagnet resets the system if the driver has not already done so. The display will indicate all black once the system resets.
The system is fail-safe since, in the event of a loss of power, only the electro-magnet is affected and therefore all trains passing will receive a warning. The system suffers one drawback in that on single track lines, the track equipment will set the AWS system on a train travelling in the opposite direction from that for which the track equipment is intended but not reset it as the electromagnet is encountered before the permanent magnet. To overcome this, a suppressor magnet may be installed in place of an ordinary permanent magnet. When energised, its suppressing coil diverts the magnetic flux from the permanent magnet so that no warning is received on the train. The suppressor magnet is fail-safe since loss of power will cause it to act like an ordinary permanent magnet. A cheaper alternative is the installation of a lineside sign that notifies the driver to cancel and ignore the warning. This sign is a blue square board with a white St Andrew's cross on it (or a yellow board with a black cross, if provided in conjunction with a temporary speed restriction).
With mechanical signalling, the AWS system was installed only at distant signals but, with multi-aspect signalling, it is fitted at all main line signals. All signal aspects, except green, cause the horn to sound and the indicator disc to change to yellow on black.
AWS equipment without electromagnets are fitted at locations where a caution signal is invariably required or where a temporary caution is needed (for example, a temporary speed restriction). This is a secondary advantage of the system because temporary AWS equipment need only contain a permanent magnet. No electrical connection or supply is needed. In this case, the caution indication in the cab will persist until the next green signal is encountered.
To verify that the on-train equipment is functioning correctly motive power depot exit lines are fitted with a 'Shed Test Inductor' that produces a caution indication for vehicles entering service. Due to the low speed used on such lines the size of the track equipment is reduced from that found on the operational network.
'Standard Strength' magnets are used everywhere except in d.c. third rail electrification areas and are painted yellow. The minimum field strength to operate the on-train equipment is 2 mT (measured 125mm (5") above the track equipment casing). Typical track equipment produces a field of 5 mT (measured under the same conditions). 'Shed Test Inductors typically produce a field of 2.5 mT (measured under the same conditions). Where d.c. third rail electrification is installed 'Extra Strength' magnets are fitted and are painted green. This is because the current in the third rail produces a magnetic field of its own which would swamp the 'Standard Strength' magnets.
Expansion of AWS application
- From 1971, an AWS permanent magnet was fitted ahead of the warning indicator where the permissible speed of a line reduced by more than a third.[8] This was a recommendation of the inquiry into the derailment at Morpeth on 7 May 1969.
- From 1977, a portable AWS permanent magnet was fitted ahead of the warning board on the approach to temporary speed restrictions (TSRs). This was a recommendation of the inquiry into the derailment at Nuneaton on 6 June 1975, which occurred when the driver missed a TSR warning board due to its lights being extinguished.
- From 1990, AWS permanent magnets were installed immediately ahead of certain 'high risk' stop signals, as a SPAD mitigation measure. This additional AWS magnet was suppressed when the associated signal showed a 'proceed' aspect. Since the introduction of the Train protection and warning system (TPWS) it is no longer current practice to use AWS for this purpose. SPAD indicators were also used.
Limitations
AWS has only two states; clear and caution. It does not provide any information about what the hazard is.
AWS is a warning system which is designed to be cancelled by the driver. It is possible for a driver on a crowded suburban railway to run all day on cautionary aspects. Continually cancelling warnings can lead to a state of conditioning, sometimes called the "double yellow zombie" effect, where the driver fails to take appropriate action when necessary. This has led to a number of fatal accidents.
It is possible for AWS to develop a wrong-side failure whereby the driver is given no indication or a 'clear' indication instead of a 'caution'. Because of this the rulebook states that "AWS does not relieve the driver of the responsibility of observing and obeying lineside signals and indicators."[1]
Also, there is no automatic brake application when a stop signal is passed. The newer TPWS, which is installed at signals where there is a risk of conflicting movements, the approach to reductions of permissible speed of more than a third and buffer stops, overcomes this problem.
Bi-directional operation

Bidirectional AWS, the permanent magnet is in the middle and there is an electromagnet both sides of it
Because the permanent magnet is located in the centre of the track, it operates in both directions. The permanent magnet can be suppressed by an electric coil of suitable strength.
Where signals applying to opposing directions of travel on the same line are suitably positioned relative to each other (i.e. facing each other and about 400yds apart), common track equipment may be used, comprising an unsuppressed permanent magnet sandwiched between with both signals' electro-magnets.
Liberia
One of the mining railways in this country had a more advanced AWS system that employed two or three magnets of either polarity and located near the rails to avoid the suppression problem. The system was therefore able to give more aspects than the BR version.[citation needed]
Other countries
The BR AWS system is also used in:
- Northern Ireland
- Hong Kong, MTR East Rail Line (only used by intercity through trains; local trains operated by MTR Corporation use TBL as of 2012, enhanced with ATP/ATO[9] - due to be upgraded to CBTC by 2020[10])
Queensland, Australia; sometimes enhanced with ATP. At the other extreme Queensland also provides a permanent magnet at the fixed distant signal of unattended crossing loops.
Adelaide, South Australia
Taiwan Railways Administration EMU100, EMU200 series (used alongside ATS-SN/ATS-P, replaced with ATP in 2006)- Experimental French system, half mechanical and half electrical (1913)[11]
See also
![]() |
Wikimedia Commons has media related to Automatic Warning System. |
- Anti Collision Device
- Automatic Train Protection
- Continuous Automatic Warning System
- Driver reminder appliance
- Intermittent Inductive Automatic Train Stop
- Train Protection & Warning System
- Crocodile (train protection system)
References
^ abcdefg "AWS & TPWS Handbook: Section 1.1.3 "The purpose of AWS"" (pdf). RSSB. Retrieved 2017-02-07..mw-parser-output cite.citation{font-style:inherit}.mw-parser-output q{quotes:"""""""'""'"}.mw-parser-output code.cs1-code{color:inherit;background:inherit;border:inherit;padding:inherit}.mw-parser-output .cs1-lock-free a{background:url("//upload.wikimedia.org/wikipedia/commons/thumb/6/65/Lock-green.svg/9px-Lock-green.svg.png")no-repeat;background-position:right .1em center}.mw-parser-output .cs1-lock-limited a,.mw-parser-output .cs1-lock-registration a{background:url("//upload.wikimedia.org/wikipedia/commons/thumb/d/d6/Lock-gray-alt-2.svg/9px-Lock-gray-alt-2.svg.png")no-repeat;background-position:right .1em center}.mw-parser-output .cs1-lock-subscription a{background:url("//upload.wikimedia.org/wikipedia/commons/thumb/a/aa/Lock-red-alt-2.svg/9px-Lock-red-alt-2.svg.png")no-repeat;background-position:right .1em center}.mw-parser-output .cs1-subscription,.mw-parser-output .cs1-registration{color:#555}.mw-parser-output .cs1-subscription span,.mw-parser-output .cs1-registration span{border-bottom:1px dotted;cursor:help}.mw-parser-output .cs1-hidden-error{display:none;font-size:100%}.mw-parser-output .cs1-visible-error{font-size:100%}.mw-parser-output .cs1-subscription,.mw-parser-output .cs1-registration,.mw-parser-output .cs1-format{font-size:95%}.mw-parser-output .cs1-kern-left,.mw-parser-output .cs1-kern-wl-left{padding-left:0.2em}.mw-parser-output .cs1-kern-right,.mw-parser-output .cs1-kern-wl-right{padding-right:0.2em}
^ "AWS & TPWS Handbook: Section 1.4 "AWS indications and their meanings"" (pdf). RSSB. Retrieved 2018-09-24.
^ "Alfred Ernest Hudd - Graces Guide". www.gracesguide.co.uk. Retrieved 2017-10-25.
^ ab "AWS and TPWS Interface Requirements: Appendix F" (PDF). rssb.co.uk. RSSB. Retrieved 2016-12-20.
^ US Patent 843550, 5 February 1907
^ Jackson, Alan A (1978). London's Local Railways. Newton Abbot, England: David and Charles. p. 99. ISBN 0-7153-7479-6.
^ Wilson, G R S (12 June 1953). Report on the Double Collision which occurred on 8th October, 1952, at Harrow and Wealdstone Station in the London Midland Region British Railways. London: HMSO. pp. 25–29. OCLC 24689450.
^ "Master Rulebook: Signals, hand signals, indicators and signs handbook. Section 7.2 "Warning indicators"" (pdf). Network Rail. Retrieved 2017-03-07.
^ MTR East Rail Line: an intro. Checkerboard Hill. March 15, 2011. Retrieved June 2, 2013.
^ "MTR awards East Rail upgrading contracts". Railway Gazette International. 21 December 2012. Retrieved 10 September 2017.
^ "New Railway Signal Experiments". The Daily News (Perth, WA : 1882 – 1950). Perth, WA: National Library of Australia. 13 December 1913. p. 4 Edition: THIRD EDITION. Retrieved 2 August 2012.
Literature
Dymond, A. W. J. (1948), "Forty years of automatic train control—the Great Western system", Journal of the Institution of Locomotive Engineers 1911-1970, Institution of Civil Engineers, 39 (207): 3–52, doi:10.1243/JILE_PROC_1949_039_007_02
Currey, J. H. (1959), "Automatic train control — the British Railway system", Journal of the Institution of Locomotive Engineers 1911-1970, Institution of Civil Engineers, 49 (267): 104–126, doi:10.1243/JILE_PROC_1959_049_013_02
Vanns, Michael A. (1997), An Illustrated History of Signalling, Ian Allan, Shepperton, ISBN 0-7110-2551-7
Simmons, Jack; Biddle, Gordon (1997), The Oxford Companion to British Railway History, Oxford University Press, ISBN 0-19-211697-5
Spowart, F. M. (March 2015). "AWS system - Introduction, Layout, Installation and Testing" (PDF). Retrieved 1 January 2018.
Further reading
Cooper, Basil (December 1981 – January 1982). "You have been warned...". Rail Enthusiast. EMAP National Publications. pp. 12–13. ISSN 0262-561X. OCLC 49957965.
jN0epv,9Iy0